
About Hide Tanning

What is hide tanning?
Hide tanning is the act of turning animal skin into textile.
Textiles are one of the oldest technologies of humanity. Animal-derived textiles predate plant-based textiles by many thousands of years. Alongside hunting and toolmaking, hide tanning has co-evolved with human community.
Natural hide tanning uses simple, organic ingredients found in a local ecosystem. Unlike modern “chem-tanning,” which relies on chromium and other to produce leather, natural hide tanning is safe and sustainable.
Types of Hide Tanning
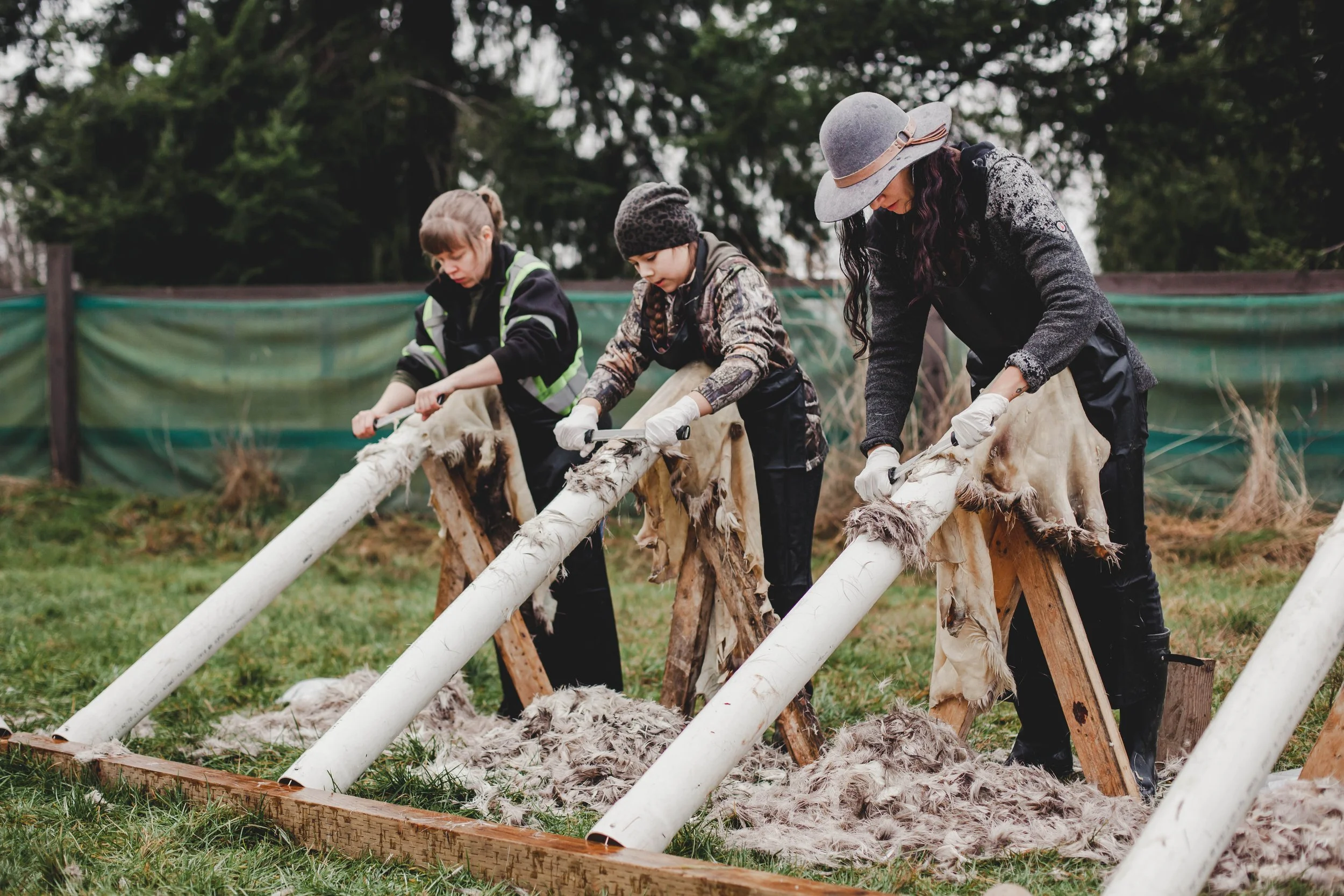
Oil-Tanning
Oil-tanning is mixing hide with oil (natural fats). Oil tanning initially preserves a hide. Over time, the oxidation of fats alters the proteins and creates a “true tanning.” Historical textiles like the chamois cloth are oil-tanned, as are sealskins. It is a common hide craft in northern and arctic climates, where fuel for smoke + tannins from trees are rare + where oxidation through temperature variation occurs readily.

Smoke-Tanning
Smoke-tanning is mixing hide with emulsified oil, then harnessing smoke to slowly sink into the hide. A natural chemical reaction occurs between smoke and lipid inside the hide, transforming it permanently. The classic soft cloth textile known as Buckskin comes from the smoke-tanning method. This method is also called brain-tanning, as animal brain is naturally emulsified (contains lecithin, the universal emulsifier).

Bark-Tanning
Bark-tanning is mixing hide with tannins extracted from plants - often, bark. Tannins are water soluble + easily move into water when heated, making a bark tea of sorts (traditionally, we call this a bark liquor). The hide absorbs tannins, which alter the proteins of the skin. A hide turns into leather before our eyes + over days and months (depending on the hide), taking on the pigment of the plant species.

Mineral-Tanning
Mineral-tanning is mixing hide with the mineral alum + salt (sodium). Alum absorbs into a hide and finds other alum molecules to lightly bond with, while keeping the skin proteins intact. Mineral-tanning does not later proteins like the methods above, making it more a preservation technique than a true tanning method. For this reason, it was historically called “tawing” to differentiate it from “true tanning.”

Tan your own!
Every animal hide can be tanned in any of the above natural hide tanning methods.
We offer beginner-friendly tanning courses online + in-person. Hides are provided by Fern + Roe. We offer rabbit, sheep, goat, and deer hides.
In our 1:1 Mentorship, we also help you work with your own hides you may have hunted or raised.